【日光化成】多様な発想とスキルを結集させ成形加工の限界を突破する
成形加工は、卓越した「成形技術」「金型技術」が必要不可欠です。「家電部品」「自動車部品」のOEMメーカーとして如何なる環境変化でも厳しい品質管理が求められてきました。日光化成ではさらに、「デザイン」、「材料開発」というユニークな技術をかけ合わすことと、AI搭載の射出成型機を設備投資し、成形加工の限界に挑んでいます。
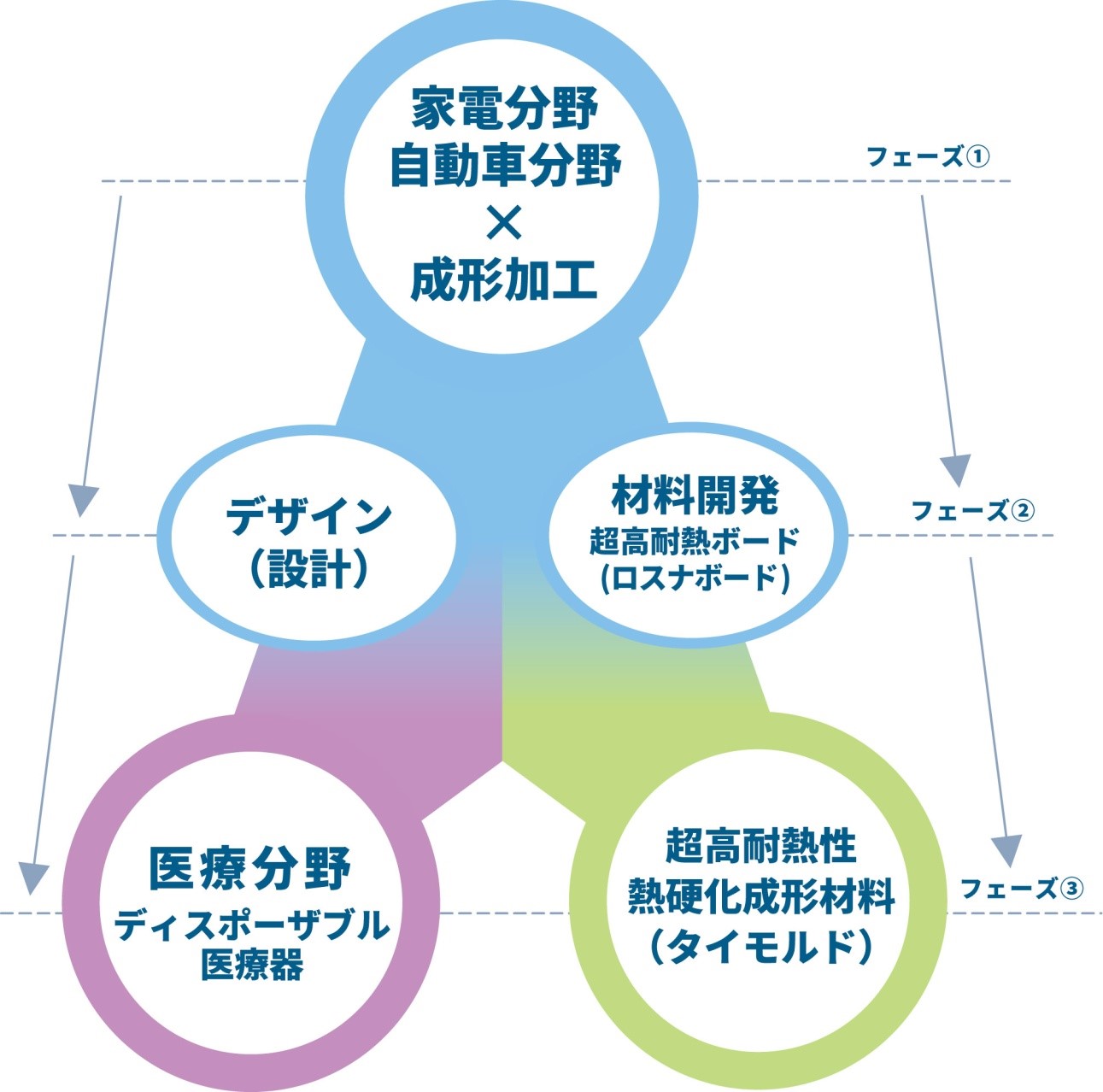
自動車×成形加工×材料開発で、成形部品の世界を変える
日光化成は、自動車部品の精密成型で、高グレードの樹脂成型を得意とするメーカーです。単なる成形加工にとどまらず、自社の技術研究所でさらに高グレードの熱硬化性樹脂材料を配合し、材料~成形加工までの一体提案を目指しています。材料の配合を知り尽くした、モルダーとして成形加工の限界に挑戦しつづけます。
≪フェイズ①≫自動車部品の成形メーカーとしてスタート
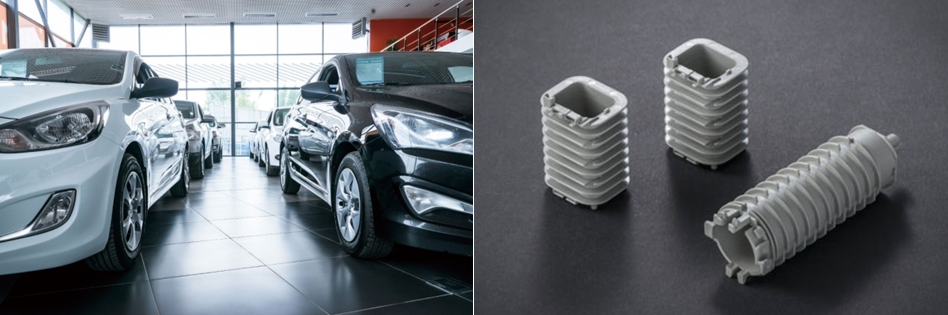
自動車の内燃機関製品各種部品を成形加工受託していました。内燃機関部品はエンジンの高温に耐える部品強度や高電圧下でも破壊しない強度を持つ部品です。業界では「重要保安部品」という名前で呼ばれ、100万個に1個でも不良品が発生しますと人命に係る事故となります。厳しい品質管理および精密な金型精度、成形加工の信頼性が要求される製品として、その成形技術金型技術を学んできました。
≪フェイズ②≫優れた配合技術をもつ技術研究所から熱硬化性樹脂の「ロスナボード」をリリース
≪フェイズ②≫優れた配合技術をもつ技術研究所から熱硬化性樹脂の「ロスナボード」をリリース

当社の耐熱ボード商品の最高グレードであり、1982年に発売されたロングセラー商品です。400度の高温の中で2万時間という過酷な条件のもとでも、形状を変えることなく、高い強度を売りにするロスナは研究開発部門の代表作品の1つで、日光化成は知らなくてもロスナボードは知っているというお声までいただくこの製品はまさに当社の原点とも言える製品です。
≪フェイズ③≫ロスナボードのノウハウを生かして、超耐熱熱硬化性成形材料「ロスナモルド」が誕生
≪フェイズ③≫ロスナボードのノウハウを生かして、超耐熱熱硬化性成形材料「ロスナモルド」が誕生
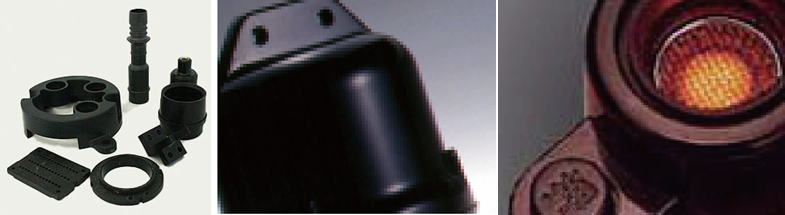
自動車内燃機関に使用する製品。高耐熱・高強度必要なため、スーパーエンプラ樹脂で
高耐熱、高環境下でも機能を発揮する「ロスナモルド」 ロスナボードの持つ高耐熱、高強度
の特性は維持しながら、「金型」で「成形」が出来るイノベーティブな製品です。インジェクション成形の他、コンプレッション成形での用途開発が可能です。
日光化成は、自動車部品精密成型で高いグレードの樹脂成形を得意とするメーカーです。受託型企業から提案型企業への変革を目指し、1970年に医療事業をスタート。同年「医療製造許可業」を取得その後医療QMSを取得、さらに医療ベンチャーを目指し、2014年医療設計部門を設置し、数々の医療機器設計に参画します。
≪フェイズ①≫家電製品の受託加工
高耐熱、高環境下でも機能を発揮する「ロスナモルド」 ロスナボードの持つ高耐熱、高強度
の特性は維持しながら、「金型」で「成形」が出来るイノベーティブな製品です。インジェクション成形の他、コンプレッション成形での用途開発が可能です。
医療×成形加工×デザインで、精密部品の世界を変える
日光化成は、自動車部品精密成型で高いグレードの樹脂成形を得意とするメーカーです。受託型企業から提案型企業への変革を目指し、1970年に医療事業をスタート。同年「医療製造許可業」を取得その後医療QMSを取得、さらに医療ベンチャーを目指し、2014年医療設計部門を設置し、数々の医療機器設計に参画します。
≪フェイズ①≫家電製品の受託加工
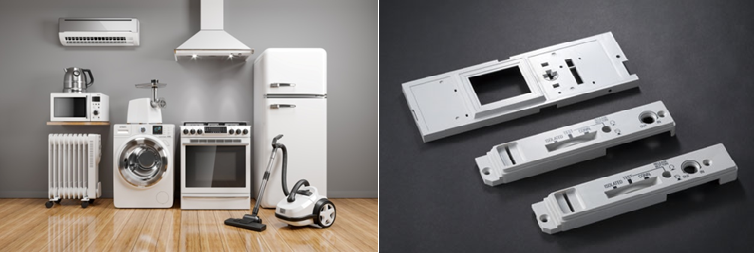
テレビ、冷蔵庫、掃除機、シェーバーなどの各種家電製品の受託加工の成形メーカーとしてスタートしました。設計や開発は家電メーカーが行い、入手した図面の仕様や材料選定、正確に再現できる金型製作とその製品製造が主業務でした。数多くの家電部品を手掛け、メイドインジャパン製品の部品加工メーカーとして、当時の家電王国日本の部品供給を保つため適格な品質管理を実施、貢献してきました。
≪フェイズ②≫設計、デザイン部門を設置
≪フェイズ②≫設計、デザイン部門を設置
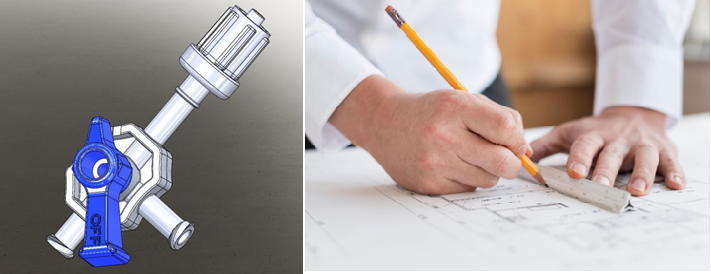
材料メーカーで設計部門を持っている企業は多くはありません。そんな中、社内で設計部門を持ち、材料の共有だけでなく、部品化までワンストップで納品できる点が大きな強みです。時には顧客のPB商品として受注することもあります。材料だけでなくデザイン力も期待されるのです。特に、医療分野では、使用されるモノが医療現場でしっかりと役目を果たし、安全であること=製品の「かたち」であることが最も重要です。人命にかかわる精密さ・正確さを要求する原点が医療部門の「設計」にはあります。このようにメーカーでありながら設計部門を有し、最終製品に近い形でのサービスを展開しています。それにより、単なるB to Bではなく、「B to B to Cを意識したものづくり」を目指し、さらに新しい材料開発のヒントをいち早く見つけ、研究開発部門にフィードバックしているのです。
≪フェイズ③≫医療ベンチャーとしてディスポーザブル医療製品が誕生
≪フェイズ③≫医療ベンチャーとしてディスポーザブル医療製品が誕生
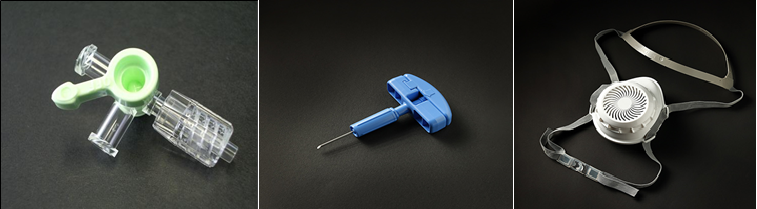
「医療製品(ディスポーザブル)」(上画像・左)
ディスポーザブル医療器の代表的製品「三方コック」。自動車の成形技術・金型技術にデザイン設計技術を加えて生まれた製品
「医療製品(金属複合ディスポーザブル)」(上画像・中央)
金属と樹脂を使う、新しいディスポーザブル製品。金属の持つ特性と樹脂の持つ特性を両方生かした製品
「医療製品(異材質複合ディスポーザブル)」(上画像・右)
医工連携で生まれた 樹脂以外の異材料を複合的にデザイン化して生まれたディスポーザブル製品。多くの高機能を集約した製品
当社では社外リソースも積極的に活用し研究開発・製品開発を行う「 オープンイノベーション」、大学の研究室を交えた「産官学コンソーシアム」などの共同開発を推進しており、日本のモノづくり技術を結集させた最先端のコンフィデンシャルな案件開発を行っています。さらにディスポーザブル医療器のビジネスはコロナ禍において医工連携へと発展しました。
様々な人や企業との出会いが新規の開発・研究事業に結びつき、当社の新しい研究や挑戦のきっかけになっています。
ディスポーザブル医療器の代表的製品「三方コック」。自動車の成形技術・金型技術にデザイン設計技術を加えて生まれた製品
「医療製品(金属複合ディスポーザブル)」(上画像・中央)
金属と樹脂を使う、新しいディスポーザブル製品。金属の持つ特性と樹脂の持つ特性を両方生かした製品
「医療製品(異材質複合ディスポーザブル)」(上画像・右)
医工連携で生まれた 樹脂以外の異材料を複合的にデザイン化して生まれたディスポーザブル製品。多くの高機能を集約した製品
次世代のテクノロジーを創造する、新たな挑戦
当社では社外リソースも積極的に活用し研究開発・製品開発を行う「 オープンイノベーション」、大学の研究室を交えた「産官学コンソーシアム」などの共同開発を推進しており、日本のモノづくり技術を結集させた最先端のコンフィデンシャルな案件開発を行っています。さらにディスポーザブル医療器のビジネスはコロナ禍において医工連携へと発展しました。
様々な人や企業との出会いが新規の開発・研究事業に結びつき、当社の新しい研究や挑戦のきっかけになっています。
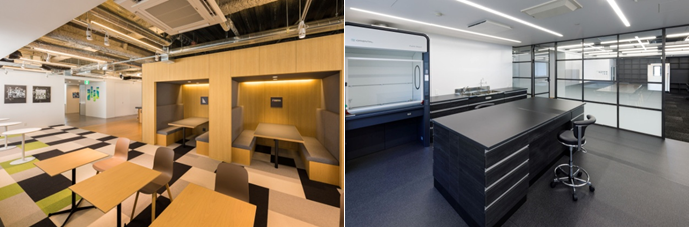
専門機関との連携も活用し技術革新。地域社会への貢献を推進する
日光化成の開発技術を支える研究所は大阪と滋賀の2拠点。大阪では医療・バイオ分野の開発を、滋賀では様々な分野の材料開発を担当しています。独自の基幹技術を磨きながら、各地区の公的研究開発機関や大手企業・地元大学とも連携し、共同研究による開発を行っています。
そうした地域に根差した研究活動が認められ、
2018 年には経済産業省「地域未来牽引企業」、
2019 年には中小企業庁「はばたく中小企業・小規模事業者300 社」、
大阪府「大阪ものづくり優良企業賞」、
2021年には経済産業省「健康経営優良法人2021」にも選定いただきました。
今後もより地域と社会に貢献し、更なる技術革新を実現できる「未来志向型企業」を目指します。
当社へのお問合せは下記「お問合せ」ボタンよりお送りください。